ARES assists the major heavy electrical manufacturer, Fortune Electric in MES implementation to connect to smart manufacturing
"Due to the order, design, and production customization business model, material control has become a critical issue." It is the bottlenecks over the years that Fortune Electric, a heavy electrical manufacturer with over half a century of history, has faced. Recently, Fortune Electric successfully implemented ARES ciMes to optimize factory production capacity and process efficiency. By building a digital management platform for smart manufacturing, Fortune Electric has improved issues such as delayed, non-transparent material records, production information and progress tracking. This has enabled transparent, data-driven, and real-time production management, gradually achieving digital transformation in smart manufacturing.
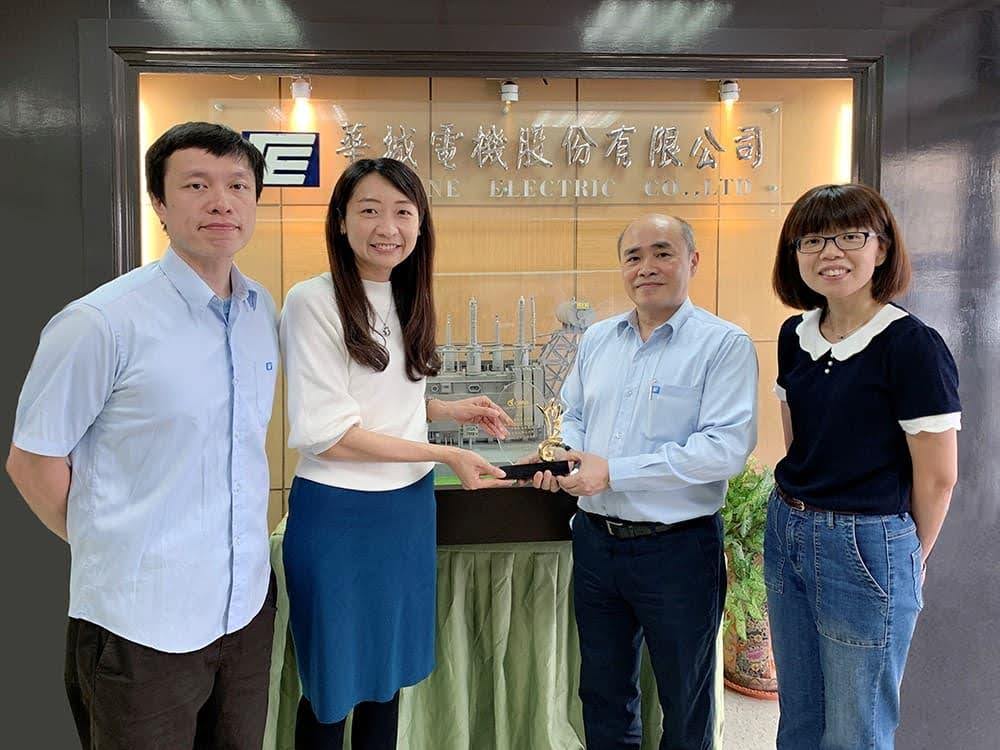
Fortune Electric's CEO, I.S.Hsu, has been considering how to integrate smart manufacturing into the factory since as early as 2015, inspired by the concept of Industry 4.0. Although the company already had some experiences with smart manufacturing before implementing ciMes, the unique characteristics of products led them to seek an MES system specifically tailored to the production processes of an electrical machinery factory, to effectively implement smart manufacturing management. Kevin Lin, Director of the Information Center at Fortune Electric, mentioned, "During the selection process for the MES system, system architecture and functionality were our primary considerations. Most MES vendors only provide a basic framework, with additional functions requiring customization costs. However, ciMes offered comprehensive functionality and a highly flexible system architecture, which was the main reason we chose ARES."
Integrating ERP and supplier systems to enhance the accuracy of information flow
Director Lin also mentioned, "ciMes functions like the spinal cord of the central nervous system, capable of connecting multiple heterogeneous systems and integrating production data from different systems, making it a key factor in ensuring smooth operations on the production line." Fortune Electric has always placed a high standard on precision in manufacturing processes and information flow. By implementing ciMes, the company has achieved internal integration with ERP system, linking work orders, part numbers, BOM and completion data. Externally, it has integrated supplier systems to reduce redundant tasks, manage supplier delivery schedules, and ensure consistency of information, thus facilitating smooth operations and production processes.
Production traceability enables real-time monitoring of production progress and enforces strict quality standards
To address the previous issues of manual production record-keeping and the lack of timely and complete tracking of production progress, PDA barcode management and WIP module played a crucial role in the implementation process. By scanning barcodes to record production information such as work orders, personnel, machines, and materials, the MES system integrates and tracks production progress in real-time, creating a production traceability record and achieving lean management. Director Lin stated that production traceability allows management to have a clearer understanding of production status, making it easier to enforce quality and standards during the tracking and inspection of materials and finished products. This effectively helps Fortune Electric improve management efficiency and reduce product defect rate.
Digital integration with suppliers enables real-time material supply, leading to transparent material management
Since the materials required for production in an electrical machinery factory are large and heavy, and the limited factory space makes it impossible to stockpile them, the arrival time of material becomes the most critical factor in the production process. By integrating with suppliers through a digital stream and the MMS module, Fortune Electric can integrate supplier material barcodes, not only collecting more detailed material information but also reflecting the usage status of materials on the production floor. This allows for real-time replenishment based on material conditions, helping to achieve transparency in material management.
Fortune Electric's IT team added, "After implementing MES, all material information must be controlled and completely recorded to maximize the effectiveness. This has also helped us streamline the supplier delivery process, solving the previous issue where materials were delivered in batches but only inspected and stored upon the final delivery."
ciMes team with high efficiency, strong collaboration, and professionalism was praised by Fortune Electric
ARES ciMes consulting team, with their extensive implementation experiences, shortening the planned implementation time from 6 months to 4.5 months, a highly efficient performance that was greatly appreciated by Fortune Electric.
The project team, composed from Fortune Electric’s Zhongli Plant and Information Center, mentioned that during the initial phase of the MES implementation, they encountered issues with the station testing process. Fortunately, the ciMes consultants were able to provide timely assistance and patiently discuss with the project managers to make the most appropriate adjustments. When there were disagreements among the on-site personnel, the consultants offered professional advices, further demonstrating the ciMes team's remarkable adaptability and expertise.
As a leading company in the heavy electrical industry, Fortune Electric continues to grow and thrive, backed by strong technical capabilities. ARES, by providing superior products and services, is partnering with Fortune to advance towards a smart factory and put smart manufacturing into practice.