Thermal Solution Leader Jentech:Implementing MES for Upgrading Smart Manufacturing
The surge of AI, electric vehicles, and the IoT has brought the thermal management industry into the market spotlight. With the increase in chip performance under high-speed computing and transmission conditions, the resulting higher heat generation has driven the demand for effective cooling solutions. Jentech, a leading thermal solution provider located in Guishan, Taoyuan, plays a crucial role as a key supplier of electric vehicle and AI server manufacturers.
Walking into the headquarter of Jentech, it is immediately greeted by display cases showcasing the company's pride—its benchmark products. "Every product producing from Jentech is a guarantee of quality. Though these components are small, they play a critical role in various industries. It may lead to significant losses for our clients when the quality issue happens" explained Alex Kuo, Vice President of the Administrative Management Center at Jentech, as he pointed to the products.
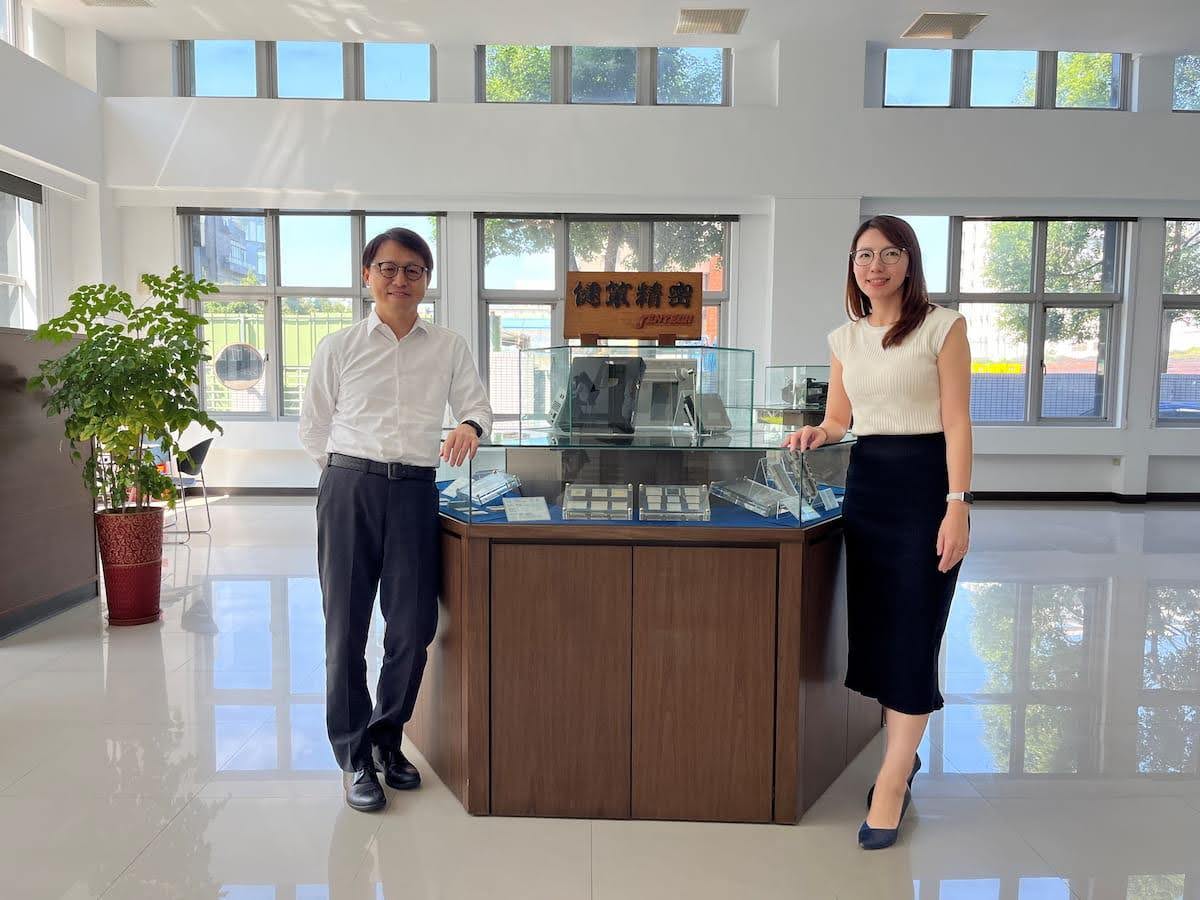
The ERP system lacked detail in production management, bringing Jentech to implement MES
At the beginning of the interview, Vice President Kuo stated, "At Jentech, MES is a crucial discipline!" Jentech initially adopted ciMes from ARES due to customer audit requirements and the leadership's visionary approach to lean management. They recognized that the ERP system lacked sufficient detail in production management and that there were no systems in place for managing work orders and production lines. As a result, Jentech decided to implement ciMes. Vice President Kuo added, "To successfully implement a system, support from managers and the appointment of a leader are essential. Without either, the momentum for implementation will be insufficient, making it difficult to fully achieve the system's potential." The managers at Jentech understand the importance of digitalization and are committed to deeply integrating it into every department. They have insisted on implementing MES across all product lines, significantly enhancing the effectiveness of the system's implementation.
Why Jentech chooses ciMes?The use of Oracle database and the consultants' industry experience
When asked why they chose ciMes, Vice President Kuo responded without hesitation, "The Oracle database and the consultants' experience in the stamping and electroplating industries!" The ciMes system uses the Oracle database, which has a more robust structure and can easily integrate with other internal systems. This has enabled Jentech to connect MES with various heterogeneous systems, such as ERP, HR, SPC, BPM, and more. This integration has automated internal operations and production processes, allowing system data to be automatically transferred, thereby simplifying the workflow for personnel.
MES Traceability as the Core to Meet Jentech's Production Line Management Needs
"MES is like the nervous system of a human, responsible for managing the entire production process at Jentech, with traceability as its core, extending outward to practical applications that align with the actual production flow and meet management needs," emphasized Vice President Kuo. He highlighted that Jentech prioritizes product quality and needs to enhance production efficiency under the correct production conditions has become the activator for extending the application of MES. "Typically, we identify pain points and frequent errors in the on-site operations. By changing our approach and finding entry points of the system, we extend its application in production management to improve on-site operations," Kuo explained as he began to share how Jentech utilizes MES in production line management.
MES Applications in Jentech
Firstly, Jentech uses MES traceability to simplify ERP workflow processes, allowing batch operations from material intake to output to be completed without creating cumbersome data in ERP. For example, during material intake, a barcode provided by the same supplier is used to retrieve production data recorded by MES, which is then transferred to the supplier platform and automatically pushed to ERP. Finally, a material barcode is automatically printed for MES. This automated process effectively reduces the workload for internal staff.
As business operations grow and product lines expand, Jentech's demand for automatic measurement equipment has increased, along with higher requirements for quality control. Through MES, inspection data from various process stages is collected, and information such as format, timing, and batch is automatically processed and transferred to the SPC system for quality monitoring. Before shipment, MES is used to check if measurement results meet the standards; only if they pass can labels be generated for shipping. This approach not only effectively controls product quality but also achieves error-proofing benefits.
What's even more noteworthy is that MES improves operational processes by integrating machines with the labeling system. When a work order enters the station, it communicates with the machine to verify the part number. Then, through the human-machine interface, MES is notified to print a label. Each item corresponds to a single label, resulting in an almost zero error rate for labeling. This integration is the starting point for Jentech's communication between MES and factory equipment and serves as the driving force for automating equipment integration.
Recently, Jentech has been further advancing its automation equipment integration applications. For example, they use PLCs to define signal meanings and then collect information such as temperature, voltage, and current for each production batch or time slot through MES. This batch recording helps understand which parameters were used to produce each product, addressing the challenge of collecting production parameters in electroplating factories. Additionally, Jentech utilizes MES for extended mold management applications, meticulously recording production history, mold lifespan, maintenance requirements, and replacement records, thereby meeting the needs of managing multiple molds on a single machine.
For Jentech, the system is a crucial part of management. Currently, MES helps Jentech with detailed recording of production history, establishing error-proofing control mechanisms, and integrating equipment data for application. When customers or the factory encounter issues, the system can also be used to resolve them, creating a positive feedback loop. In the future, Jentech will continue to deepen MES applications, develop intelligent reports for data analysis, and enhance data insight capabilities to support management decisions. As a leader in digital transformation, Jentech aims to seize business opportunities in the electric vehicle and server markets.