TXC Saves 50% of Production Cycle Time, Advancing towards Wafer-level Production Process with ARES ciMes.
Quartz components are like the "pulse" of electronic products, controlling frequency and connecting all parts to function effectively, enabling electronics products smooth operation. They can be found in various products such as smartphones, laptops, cars, and networking devices. TXC Corporation, a leading quartz component manufacturer located in Pingzhen, Taoyuan, is capitalizing on the advancements in 5G communications, Wi-Fi, artificial intelligence, and smart vehicles. Through industry-leading manufacturing process capabilities, the company is developing semiconductor wafer-level processes to produce more "miniaturized and high-precision" quartz components, making it an indispensable key player in the tech and electronics industry.
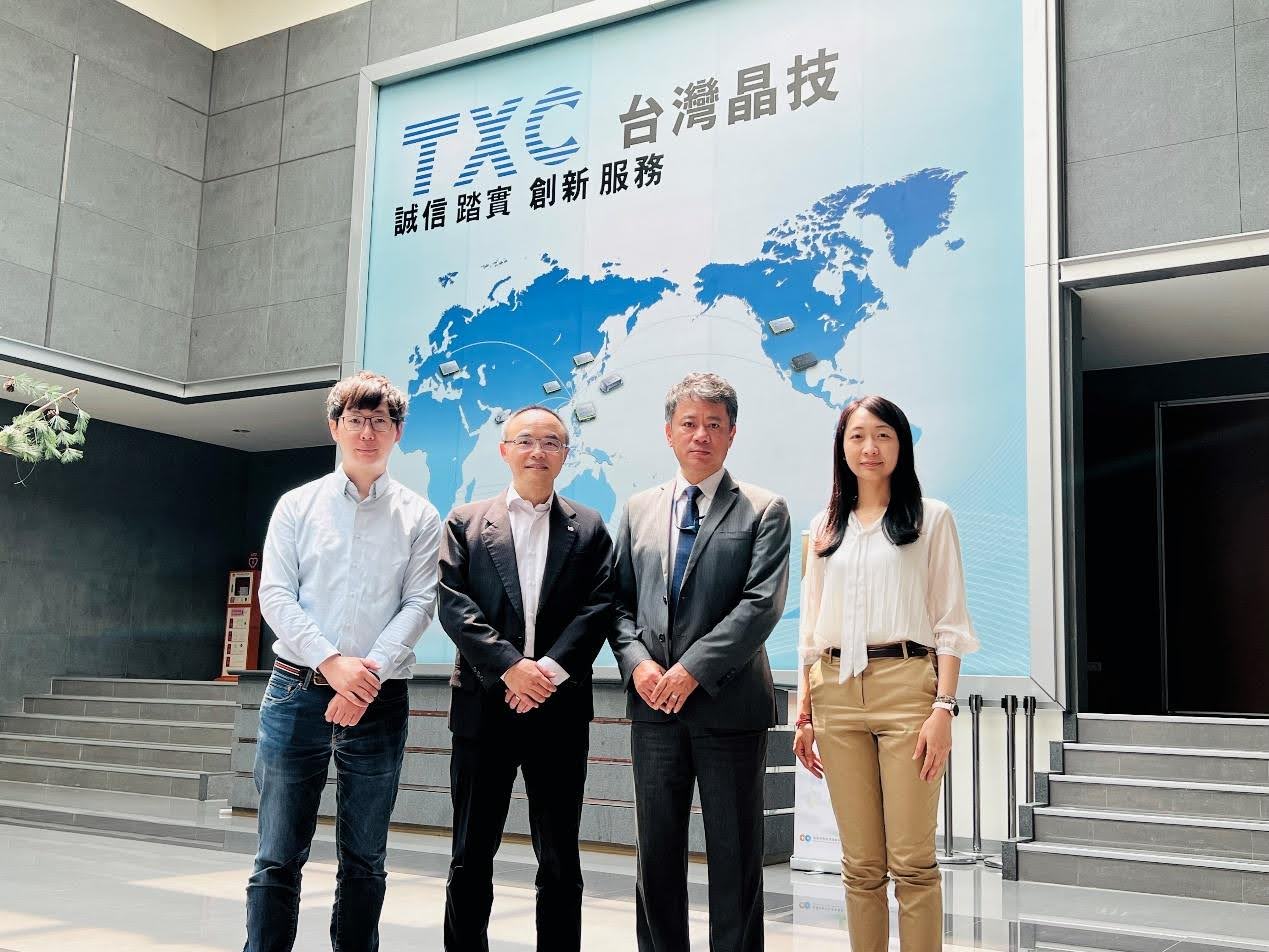
MES assists automated equipment in real-time management and monitoring of production processes
"In recent years, in response to market applications and demand, we have begun implementing wafer-level production processes. To achieve this, highly automated equipment is required, and these automated systems indeed need a precise system to control the entire production process. Therefore, we decided to introduce a smart factory and MES (Manufacturing Execution System) to assist the automated equipment in carrying out advanced production," said Li-Wei Cheng, Vice President of the MEMS Center at TXC Corporation, as he gestured to the various process diagrams displayed in the conference room.
In the management of a smart factory, the integration of automation combined with the MES and data platform processing are critical elements. In the past, TXC discovered unnecessary downtime during production, leading to resource waste, extended cycle times, and difficulties in meeting order deadlines. Additionally, they recognized the need for digitalized management of production information such as work-in-progress, machines, materials, process recipes, and specifications to assist managers in making precise decisions.
Vice President Cheng added, "At that time, we realized that if we could establish manufacturing information on a comprehensive production platform, with all personnel and systems operating according to the MES manufacturing system, we could reduce cycle times, lower costs, and complete troubleshooting. This is how real-time factory management can truly be achieved."
The ciMes system's features, consulting expertise, and service quality have won the favor of TXC
Kevin Chen, Vice President of the Management Center at TXC Corporation, shared the process of selecting an MES vendor and the criteria they used to make their decision.
- Product Functionality:The most important factor in choosing an information application system is whether its features meet the company’s needs.
- Consultant Industry Experience:The vendor's consulting team should have sufficient professional knowledge and relevant industry experience to facilitate effective communication.
- Service Quality: It’s essential to review feedback from the vendor's previous clients to assess the service quality and reputation.
Overall, from system functionality and consultant industry experience to customer services, ARES was identified as a well-developed, experienced, and customer-oriented MES vendor. Based on this, TXC decided to implement the ciMes with ARES.
TXC Implements 9 Product Modules of ciMes
"MES is like our heart, or the lifeblood of our body. Through the system, we can fully grasp everything happening in the factory," Vice President Chen said with conviction. This time, TXC implemented ARES's ciMes, utilizing its nine product modules. The system focuses on work-in-progress management and traceability, extending its application outward to integrate management information from the production floor, including production, quality, and key machinery. A comprehensive monitoring mechanism was established, and with the use of electronic kanban system, managers can now monitor production progress in real-time, meeting all management needs.
ciMes consultants tackled each challenge during the system implementation process
However, the system implementation process was not smooth sailing, as various unexpected situations and challenges arose. One of the most memorable experiences for Vice President Kevin Chen was when an issue occurred with equipment provided by an overseas vendor. The ciMes team had to work closely with the TXC team, liaising with the equipment vendor, holding meetings and conducting repeated on-site tests until the problem was resolved. This experience demonstrated the ARES team's commitment to customer service, their thorough problem-solving approach, and their professional technical capabilities, which were crucial for the successful deployment of the system.
Vice President Li-wei Cheng from the MEMS Center also mentioned that introducing any system is like a racing competition with time. ciMes team should understand our industry know-how and needs by communicating with users within a short time. When dealing with users who are encountering the system for the first time, ciMes consults are also very patient in teaching, allowing our colleagues at TXC to understand the system in the shortest time. Another crucial aspect is that when our colleagues encounter significant issues during operation, ciMes consultants are always able to coordinate all resources to resolve problems on the production line. This demonstrates the professionalism and immediate response capability of the ciMes team.
ciMes brings benefits to TXC
After implementing MES and equipment automation, TXC’s factory has gained numerous tangible benefits:
- Real-time tracking of production management and process digitalization increased visibility by 95%
- Production cycle time was reduced by 50%
- Production capacity increased, and manufacturing costs were reduced by 30%
- Equipment automation reduced production labor by 40%
- Data and reports are generated automatically, saving 10% of manual data organization and analysis time
- Optimized management indicators: Scheduling optimization improved order fulfillment rate, productivity, and product quality.
For TXC, smart manufacturing is fundamentally about pursuing product quality, continuously improving yield rates, and significantly enhancing overall manufacturing costs and operational performance. This enables a rapid response to customer and market demands. With the completion of the MES system implementation, the next step is to improve the collection and analysis of big data. This involves developing artificial intelligence based on data and integrating it with existing IT systems to optimize the company's overall operational performance. These applications will also provide feedback on how to improve current workflows and how to revise production equipment specifications, serving as a foundation for creating customized production equipment in the future. This approach allows TXC to maintain its existing competitive advantages while offering customers higher quality, lower costs, and better product functionality and services.